An Electric Giant
Liebherr has opted for electrical drives for their largest material handling machines. In order for the electricity to flow to the drive systems without any maintenance, the cabling needs to withstand quite a lot.
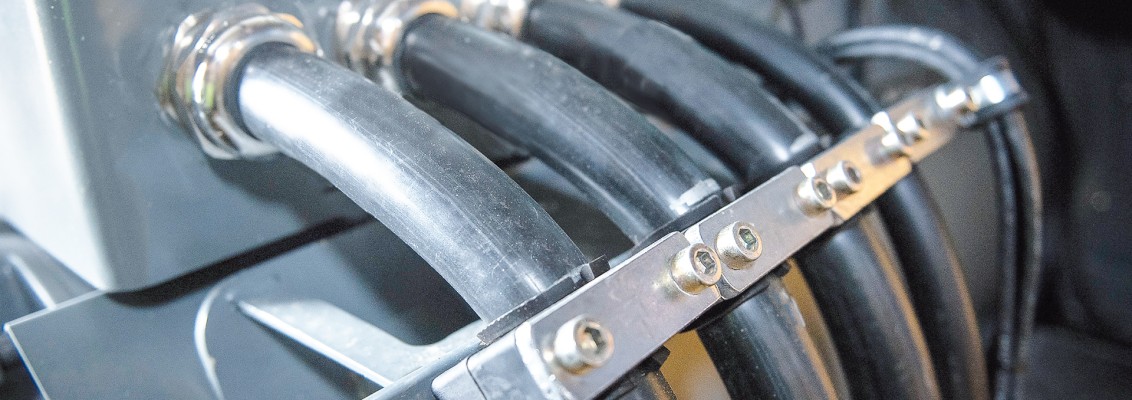
At a first glance, the new Liebherr machine looks like a conventional tracked excavator. Just a bit taller, perhaps. This is because the machine was first seen from a distance of almost 100 metres (328 feet), and there is nothing nearby that can serve as a benchmark for the eye. At a second glance, at close range, the differences become more obvious. This machine is so high that the excavator operator could look down into the skylight of a typical terraced house. And he could reach out over the gable with the boom, and dig up half the garden in a single shovel load – without even touching the chimney even once. This will never happen, however. Strictly speaking, this yellow giant with the designation LH 150 EC High Rise is not an excavator, but is one of the so-called material handling machines – and these are intended for larger tasks. Tobias Riedmiller, who is responsible for the development of the new machines at Liebherr, explains, “With the development of our new large excavators, we are responding to the growing importance of global bulk commodity handling. In maritime and inland ports, or in scrap, timber or steel processing, increasing importance is being placed on low noise and exhaust emissions. In addition, the infrastructure there is already laid out for electricity, instead of diesel. We have therefore developed a completely new platform for the electrical drive, based on the previous LH 120 model.” According to Tobias Riedmiller, additional advantages of the electrical drive are a significantly lower maintenance requirement and thereby higher productivity.
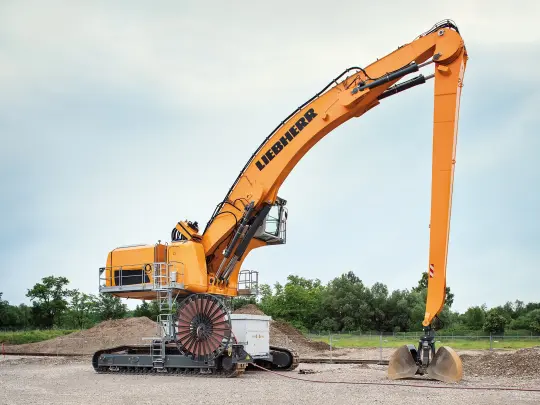
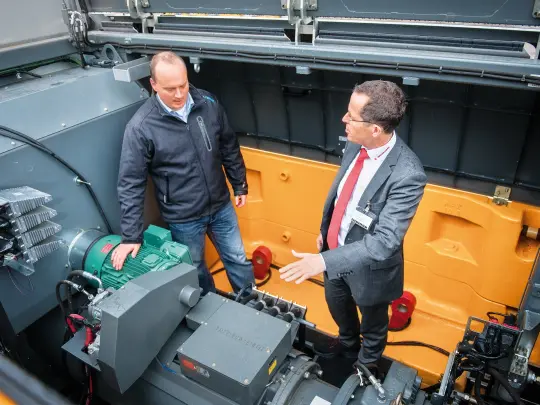
REDUCING CARDIAC FAILURE TO ZERO
In order for this giant to apply its 536 horsepower to the boom so that up to 1,000 tons of material per hour can be moved within a turning radius of about 30 metres (100 feet), it is cabled and supplied with 20,000 volts of medium voltage. This has to be transformed into a voltage that can be used by the electric motors, so a powerful transformer and a frequency converter are thereby mounted on board the excavator. The current flows from there directly into the machine room. Daniel Bayer, who was responsible for the development of the electrical drive system, explained that the cable connections of the drive system are the “coronary arteries” of the material handling machine. In order to reduce the risk of heart failure to a minimum, a cable is needed that can withstand the special conditions and meets the high-quality standards. The conditions for this kind of performance are rough. Very tight bending radii, high UV-resistance, strong vibrations, and exposure to aggressive substances such as hydraulic oils put a great deal of demand on the cable jacket and the connections. “We produce for the global market. Therefore, the excavator must be designed to carry out its work in the Finnish winter at minus 30 degrees, as well as in the scorching heat of Dubai. The cabling must also withstand these extreme temperatures,” explains Daniel Bayer.
CABLES PUT THROUGH THEIR PACES
With these requirements in mind, Daniel Bayer called on HELUKABEL in July 2012. “HELUKABEL has established itself as a reliable partner of the Liebherr Group for many years. It was therefore only natural to ask them first,” he said, recalling his first telephone conversation with Joachim Koch, who works in the Custom Cables Department. A cable that could meet the technical requirements was quickly identified from the comprehensive product range – HELUWIND, a cable with a diametre of 400 mm (750 kcmil), which was originally developed for use in a wind turbine’s cable loop. The mechanical properties that had been integrated by the developers formed the perfect starting point for the tasks of the material handling machine. The cable thereby fulfilled a number of features from the very start such as a vast operating temperature range, UV resistance, and the bending radii required for the design. Unlike its use in wind turbines, the cable in the Liebherr application would not be exposed to torsion, but to strong vibrations. “The question now was whether this cable would also be suitable as a screened, motor connection cable and connect to the frequency converter. “In order to find out, we had to subject the cable to numerous mechanical and electrical tests,” said Joachim Koch. Liebherr developer Daniel Bayer added, “The mechanical loads, and above all the resistance to aggressive substances such as oils, greases and coolants were the crucial points. This was crucial because we wanted to ensure the motor cabling required no maintenance over the entire service life of the handling machine.
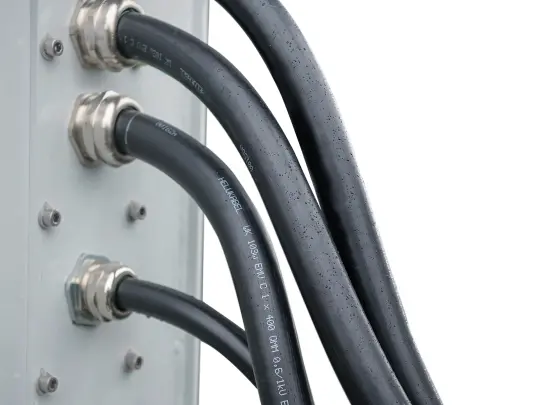
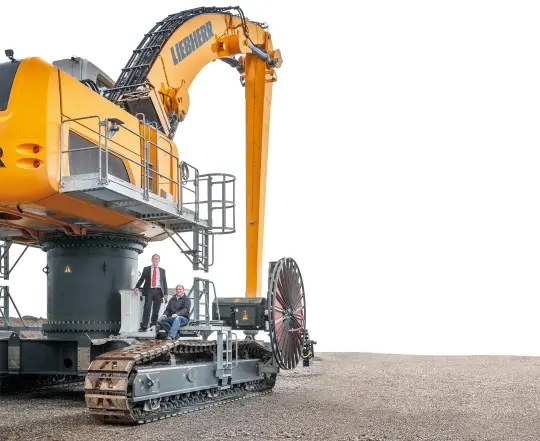
WARDING OFF THE ATTACK FROM THE AGGRESSIVE SUBSTANCES
Initial testing with sample oil specimens took place as early as November 2012. “For our tests, Liebherr provided us with both synthetic oils and biological oils produced from renewable raw materials, which are significantly more aggressive on plastics than conventional oils on a mineral basis,” recalls Joachim Koch. The tests took place in accordance with VDE. The cables were exposed to the oils at a temperature of 90 degrees Celsius (194 Fahrenheit) for seven days. The inspectors then determined the remaining tensile strength and elongation at break. In order for the cables to be able to withstand all the mechanical loads during operation, special attention also has to be paid to the cable clamps. “We have developed our own vibration plate in our test centre, which realistically simulates the loads that arise on large machines,” reported Joachim Koch. In extensive tests, the clamps proved their readiness for use.
All the test procedures, including determination of flame resistance, were completed by the end of 2012. Test results concluded that the HELUWIND cable is ideally suited for being both a motor connection cable and connecting to the frequency converter in the Liebherr electrical handling machine, and the order was placed in February 2013. “Through extensive testing during the design phase, we were able to avoid problems in the actual prototype phase. This accelerated the whole process,” said Liebherr developer Daniel Bayer with satisfaction. He added: “HELUKABEL has once again excelled as a reliable and responsive development partner.“
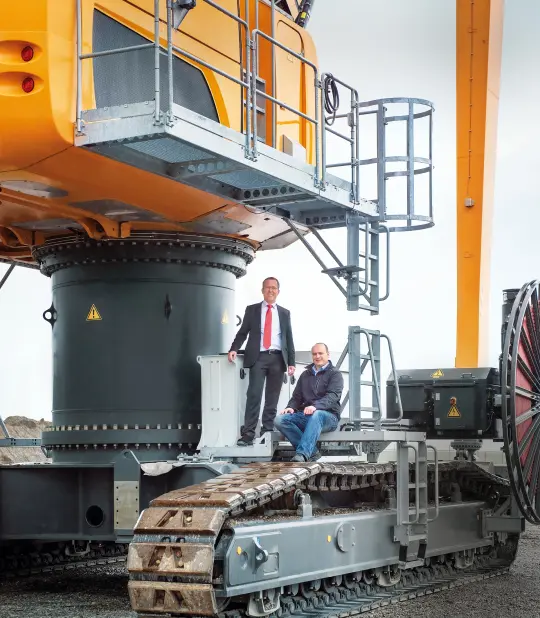
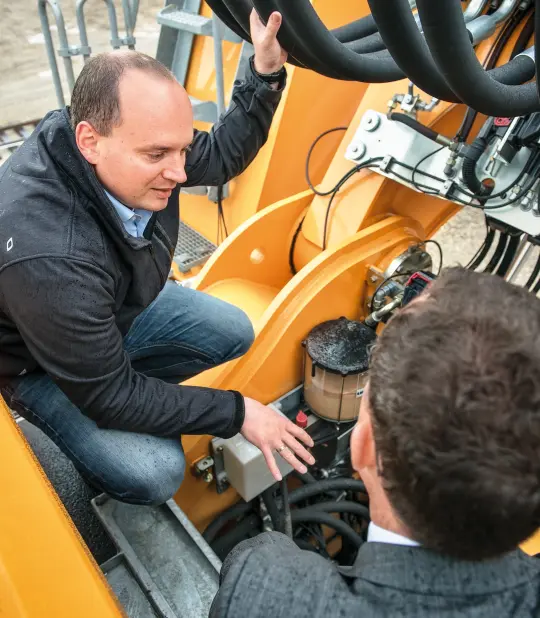